Em setembro, a Dow declarou um marco em seu esforço para mitigar o fluxo de resíduos plásticos. A grande indústria química e a Mura Technology encerraram um projeto em Böhlen, na Alemanha, para construir uma planta baseada no processo de vapor supercrítico de Mura. A instalação converterá resíduos plásticos mistos em líquidos de hidrocarbonetos que a Dow carregará em seu cracker de etileno no local para conversão de volta em novos plásticos.

Em meio a polêmica, indústria aposta na pirólise de plásticos
A planta será a maior do gênero na Europa, desviando 120.000 toneladas métricas (t) de resíduos por ano dos incineradores. Será seis vezes o tamanho da primeira fábrica de Mura, ainda em construção em Teesside, Inglaterra. Os parceiros esperam construir instalações adicionais nas instalações da Dow na Europa e nos EUA para um total de 600.000 t de capacidade anual.
“A Böhlen é uma espécie de caso básico, e só aumentará a partir daí”, disse Oliver Borek, diretor comercial da Mura, durante uma coletiva de imprensa. Um executivo da empresa de engenharia KBR, que está licenciando o processo além da Dow e Mura, observou que sua empresa já está projetando três plantas na Coreia do Sul e uma no Japão.
Os fabricantes petroquímicos estão totalmente por trás da ampla gama de processos de pirólise, como o de Mura, em desenvolvimento em todo o mundo. Quase todas as grandes empresas químicas – Dow, BASF, Shell, ExxonMobil, LyondellBasell Industries, Sabic, Ineos, Braskem e TotalEnergies, para citar algumas – se uniram a uma empresa menor desenvolvendo um processo ou está criando seu próprio.
Essas empresas argumentam que a pirólise pode compensar as deficiências da reciclagem mecânica, o processo familiar de lavar e repelir os plásticos que os consumidores jogam nas lixeiras azuis. Apenas dois polímeros – o tereftalato de polietileno (PET) encontrado em garrafas de refrigerante e água e o polietileno de alta densidade em jarras de leite e outros recipientes – são amplamente reciclados em uma escala apreciável. E é difícil obter mesmo esses materiais relativamente homogêneos até as especificações de contaminação necessárias para uso em contato com alimentos. Ao todo, a reciclagem mecânica consegue capturar apenas cerca de 9% dos plásticos nos EUA, de acordo com a Agência de Proteção Ambiental dos EUA.
Os recicladores podem lidar com mais algumas resinas com processos de despolimerização que decompõem os polímeros em seus precursores químicos. Por exemplo, a metanólise pode ser usada para reciclar produtos PET, como fibras e folhas, que não são passíveis de métodos mecânicos. E as empresas vêm quebrando o nylon usando hidrólise há muitos anos.
Mas a maior parte dos plásticos que usamos – embalagens de doces, sacolas, sacos de batatas fritas, embalagens protetoras, copos descartáveis, sacos de alimentos congelados, lâminas de barbear, tubos de pasta de dente, cotonetes e outros objetos de nossas vidas diárias – desafiam tanto a reciclagem mecânica quanto a despolimerização.
Esses itens são construídos a partir de vários plásticos que são quase impossíveis de separar. Além disso, eles são feitos principalmente de poliolefinas como polietileno e polipropileno, que possuem fortes ligações carbono-carbono que resistem à despolimerização. Para esses plásticos mistos, a pirólise é a única ferramenta atualmente viável da indústria para recuperar matérias-primas e fabricar novos polímeros.
Mas um reator de pirólise não é uma caixa mágica que pode fazer desaparecer os problemas de resíduos da indústria de plásticos. O processo é superficialmente simples: usar altas temperaturas na ausência de oxigênio para quebrar o plástico em uma mistura de moléculas menores conhecidas como óleo de pirólise. No entanto, converter os diferentes tipos de plásticos que podem acabar como resíduos em uma matéria-prima não contaminada – como as parafinas C 5 – C 12 que seriam uma matéria-prima de nafta ideal para um cracker de etileno – apresenta desafios consideráveis. As empresas de plásticos precisarão superar esses desafios se quiserem desmascarar as objeções dos ambientalistas e cumprir suas próprias metas de redução de resíduos e emissões de carbono.
O CALDEIRÃO DE PIRÓLISE
“Às vezes, brincamos que todos os dias precisamos fazer um bolo de aniversário, mas os ingredientes mudam o tempo todo, e é melhor que o bolo de aniversário seja bom e tenha o mesmo sabor”, diz Eric Hartz, cofundador e presidente da empresa de pirólise. Circular Nexus. “Há um tipo de arte acontecendo aqui ao lidar com insumos heterogêneos em oposição a homogêneos. Não há uma ciência perfeita sobre por que alguns compostos se comportam da maneira que se comportam nesses ambientes”.
PIRÓLISE
Esse caminho apoiado pela indústria para a circularidade dos plásticos decompõe quimicamente os plásticos em seus componentes para que possam ser transformados em novos plásticos.
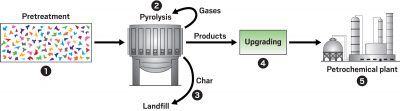
Crédito: Alex Tullo/Will Ludwig/C&EN
1. Pré-tratamento
A matéria-prima para plantas de pirólise é composta idealmente por poliolefinas, como polietileno e polipropileno. Materiais errantes como tereftalato de polietileno contendo oxigênio e cloreto de polivinila carregado de cloro são removidos.
2. Pirólise
Os plásticos são aquecidos a cerca de 500°C na ausência de oxigênio. As moléculas mais longas se quebram em frações líquidas como nafta e diesel, cortes sólidos como ceras e gases de menor peso molecular. Na maioria das fábricas, cerca de 10% do produto é carvão, um subproduto.
3. Descarte de aterros sanitários
O carvão é transportado para o aterro ou pode ser adicionado ao asfalto ou concreto. A maioria das plantas queima os gases para obter calor.
4. Atualizando
Para que a saída seja adequada para a fabricação de novos plásticos, adsorventes e hidroprocessamento podem ser necessários para remover cloro, nitrogênio e outros poluentes. Um hidrocraqueador, ou unidade similar, às vezes é necessário para quebrar ainda mais as moléculas grandes.
5. Usando resíduos
A nafta é processada em um cracker de etileno para criar etileno e propileno, blocos de construção para mais polietileno e polipropileno.
Um desafio da pirólise é a variabilidade da matéria-prima. Os diferentes polímeros que são alimentados em um reator de pirólise quebram em diferentes padrões. Em particular, moléculas com alto grau de ramificação racham mais facilmente do que as lineares.
De acordo com um artigo de revisão do engenheiro de bioprodutos e biossistemas da Universidade de Minnesota Twin Cities Roger Ruan e outros cientistas, o polipropileno se decompõe a 378–456 °C, enquanto o polietileno de baixa densidade se decompõe a 437–486 °C e o polietileno de alta densidade em 452–489°C. Como resultado, as empresas que processam resíduos plásticos mistos devem selecionar uma temperatura – normalmente acima de 500 ° C – na qual todos os polímeros que absorvem em um determinado dia se decompõem.
No entanto, a temperatura afeta a composição da saída de uma unidade de pirólise. A pirólise produz líquidos úteis, como nafta e diesel. Mas também cria ceras menos desejáveis que podem precisar ser decompostas ainda mais. E a pirólise produz gases mais leves que normalmente são queimados como combustível no reator. Altas temperaturas e longos tempos de residência do reator podem reduzir a produção de cera e produzir mais nafta, mas também criam gases que têm utilidade limitada.
Altas temperaturas também podem levar à desidrogenação, ciclização, aromatização e reações Diels-Alder, criando assim mais aromáticos. “Para combustíveis e assim por diante, tudo bem”, diz Ruan. “Mas às vezes queremos matéria-prima de nafta para a produção de novos plásticos; não queremos muitos aromáticos.”
E alimentar os plásticos errados em reatores de pirólise cria ineficiência e pode contaminar a saída. O PET contém oxigênio e tende a formar dióxido de carbono, diz Ruan. O cloreto de polivinila (PVC) produz compostos clorados. Além disso, alguns plásticos têm muitos aditivos inorgânicos, como negro de fumo, carbonato e argila. Eles levam à formação de carvão, que os operadores de pirólise devem descartar como resíduo sólido.
AMBIENTALISTAS RECLAMAM
Os ambientalistas detestam a pirólise. E um número crescente de jurisdições, como a Califórnia, não considera reciclagem alguma . Um crítico é Jan Dell, um engenheiro químico que fundou e dirige a Last Beach Cleanup, uma organização ambiental. Ela ajudou grupos ambientais maiores, como o Conselho de Defesa dos Recursos Naturais e o Greenpeace, a preparar relatórios sobre a prática. Para apresentações, a Dell compilou 16 páginas de objeções.
Uma das principais queixas da Dell é que as instalações de pirólise não podem realmente aceitar os resíduos plásticos misturados que afirmam que podem. O PVC, PET e outros materiais residuais no fluxo atrapalham demais o processo.
“Existem muitos tipos”, diz Dell. “Há muitos aditivos. Você não pode reciclá-los todos juntos, e separá-los desafia a segunda lei da termodinâmica. É simplesmente impossível reordenar – como Humpty Dumpty – todos esses plásticos depois de colocados em uma lixeira na calçada.”
A Dell afirma que a Renewlogy, uma empresa sediada em Utah que estava desenvolvendo uma planta de pirólise, fechou exatamente por esse motivo. Seus marcadores contêm até uma foto de uma instalação Nexus Circular em Atlanta mostrando fardos de filme plástico relativamente limpo do tipo usado em armazéns – evidência, ela diz, de que a empresa não está aceitando muitos resíduos plásticos mistos pós-consumo.
Uma segunda acusação é que a pirólise é realmente incineração, embora os reatores de pirólise operem na ausência de oxigênio. “Se você olhar apenas para o próprio vaso de pirólise, não, não há queima. Tenho que concordar com isso”, diz Dell. “Mas aqui está o negócio: como você aquece aquele recipiente de pirólise para os 900 a 1.500 ° F que você precisa? Você o aquece incinerando o gás que sai dele.”
A Dell aponta para a indústria de pirólise Brightmark, que divulgou à EPA que 70% da produção de uma planta que está construindo em Ashley, Indiana, serão gases que planeja usar para energia ou queima. A Brightmark agora diz que esses números foram enviados por engano. Esses gases representam apenas cerca de 18% da produção, diz a empresa, e está apresentando o número atualizado à EPA.
Outra crítica tem a ver com a escala. A Dell diz que cerca de 120.000 t por ano de pirólise e outras capacidades de reciclagem química estão atualmente em produção nos EUA. Isso representa uma fração minúscula da produção total de plásticos de cerca de 56 milhões de toneladas na América do Norte em 2021, de acordo com o Conselho Americano de Química. Apenas uma nova planta de polietileno tem cerca de 500.000 t de capacidade anual.
Para críticos como a Dell, a pirólise é um esquema de lavagem verde destinado a enganar o público, fazendo-o pensar que os plásticos são mais reciclados do que realmente são. Ela ressalta que a indústria, sob pressão semelhante no início dos anos 1990, construiu muita capacidade de reciclagem, apenas para fechá-la quando os projetos se mostraram inviáveis e a atenção do público se desvaneceu. A indústria agora está repetindo esse padrão, diz a Dell.
A INDÚSTRIA AVANÇA
Executivos do setor dizem que estão mais comprometidos do que nunca com a reciclagem e estão ansiosos para praticar a pirólise em larga escala. Suas empresas estão construindo instalações maiores do que antes e as estão testando no mundo real. Eles estão cientes das rugas em um sistema de reciclagem baseado em pirólise e dizem que estão determinados a eliminá-las.
Manav Lahoti, diretor global de sustentabilidade para hidrocarbonetos da Dow, diz que a experimentação melhorará os sistemas a longo prazo.
“Às vezes você adota essa abordagem onde há sucessos e depois há fracassos e você se concentra singularmente nos fracassos e diz: ‘Ah, não está funcionando’”, diz ele. “Existe um impulso com empresas como nós para realmente criar uma solução para esse desafio? A resposta é sim. E então, ao longo do caminho, você terá alguns sucessos e alguns fracassos.”
A Brightmark está enfrentando sua parcela de obstáculos. A planta que a indústria está inaugurando em Indiana, ao custo de US$ 260 milhões, foi projetada para converter 100.000 t de resíduos plásticos mistos por ano em nafta, diesel e ceras industriais.
No final de 2020, Bob Powell, CEO da Brightmark, disse que a construção da instalação estava 80% concluída e pronta para aumentar a produção em 2021. Mas em abril de 2022, a empresa havia fabricado apenas cerca de 2.000 t de produto. Agora Powell diz que será executado em grande escala no próximo ano.
“O maior desafio neste momento tem sido o COVID”, diz Powell. A pandemia atrasou a entrega dos equipamentos e dificultou a contratação de mão de obra suficiente para trabalhar na fábrica. A empresa também sofreu um incêndio em maio de 2021 que chama de “pequeno contratempo” em um e-mail.
Em outro revés, a Brightmark cancelou os planos de construir uma fábrica de US$ 680 milhões em Macon, Geórgia, que seria quatro vezes o tamanho da fábrica de Ashley. A fábrica enfrentou oposição local. E a Brightmark estava contando com cerca de US$ 500 milhões em títulos da Autoridade Industrial do Condado de Macon-Bibb, mas o acordo estipulava que a Brightmark iniciasse a fábrica de Ashley, e o condado retirou seu apoio depois de determinar que a empresa não teve sucesso em Indiana.
Powell diz que a Brightmark foi tratada injustamente. “Essas são perguntas que eu acho que com um tour pelas instalações que as pessoas poderiam ter respostas muito rapidamente”, diz ele.
A Brightmark, pioneira na pirólise, também teve que lidar com a evolução das demandas do mercado, de acordo com Powell. Quando a empresa começou a construir suas instalações em 2019, a principal preocupação era desviar os plásticos do fluxo de resíduos. A produção de nafta e diesel foi destinada ao mercado de combustíveis.
“Nos 3 anos seguintes, a demanda por plásticos totalmente circulares cresceu exponencialmente”, diz ele. Agora, a Brightmark pretende vender nafta para empresas químicas como matéria-prima de plásticos e quer que seu diesel acabe também nos mercados químicos.
Devido a essa crescente demanda por matéria-prima reciclada, o Nexus Circular está recebendo muita atenção dos grandes fabricantes petroquímicos. A planta da empresa em Atlanta tem capacidade anual de 13.000 t. Cerca de 80% de sua produção é o que Hartz descreve como uma mistura de nafta, gasolina, diesel e ceras mais pesadas. O resto são gases que o Nexus usa para aquecer.
A Shell e a Chevron Phillips Chemical já estão usando a produção da planta Nexus em seus crackers petroquímicos nos EUA. A Dow concordou em receber a produção de uma planta em Dallas que terá o dobro do tamanho da planta de Atlanta. A Nexus também pretende construir uma unidade de 30.000 t em Chicago que abastecerá a Braskem, um de seus investidores.
Hartz diz que uma coisa que diferencia sua empresa é que ela pode lidar com diferentes formas de plásticos, como filmes geralmente difíceis de reciclar, com pré-classificação limitada. Tampouco precisa processar sua produção com destilação ou hidrotratamento, o que, segundo ele, “adiciona custos tremendos”, além de carga ambiental.
Hartz admite alegremente o ponto de vista da Dell de que o Nexus é meticuloso sobre os resíduos de plástico que consome. Para evitar a triagem e o pós-processamento, a empresa se concentra na aquisição de fluxos de poliolefinas relativamente homogêneos, como embalagens de paletes de varejistas. Embora esses materiais possam não se encaixar na ideia de plásticos pós-consumo de todos, diz Hartz, eles ainda estavam destinados ao aterro sanitário.
A Nexus paga um prêmio por esses plásticos em comparação com o lixo doméstico misto. “Eles não são gratuitos se você quiser a qualidade certa”, diz Hartz. “Se você quer lixo, terá que configurar um processo muito, muito caro antes mesmo de poder usá-lo.”
PREPARANDO-SE PARA A PIRÓLISE
Muitas outras empresas estão adotando essa abordagem e tentando obter mais resíduos mistos. “Se você fala sobre a verdadeira circularidade em escala, você está falando sobre resíduos plásticos mistos; você não está falando de poliolefinas pré-classificadas”, diz Artem Vityuk, gerente de mercado global da BASF. “Você está realmente tentando expandir a base de matéria-prima e precisa ser capaz de trabalhar com ração realmente contaminada.”
Isso significa que a produção de unidades de pirólise que consomem uma ampla variedade de plásticos deve ser atualizada para eliminar a contaminação. A BASF lançou recentemente um novo portfólio, chamado PuriCycle, de catalisadores e adsorventes que eliminam esses contaminantes. O portfólio visa plantas de pirólise que tentam atender às especificações dos clientes e empresas petroquímicas que desejam limpar matérias-primas provenientes de várias fontes.
Vityuk explica que contaminantes como halogênios, oxigênio, nitrogênio e metais são encontrados nos hidrocarbonetos que saem das plantas de pirólise. “Isso é o que está nos plásticos”, diz ele.
Esses contaminantes podem ser irritantes. Um cracker de etileno pode tolerar apenas 1 ppm de cloro em sua alimentação, portanto, mesmo um pedaço de tubo de PVC na entrega diária de um reator de pirólise pode causar problemas para um cliente de uma empresa química. A BASF oferece adsorventes para absorver os compostos de cloro. A linha de produtos também inclui adsorventes e catalisadores de pré-hidrogenação comercializados como capazes de filtrar material particulado e eliminar os compostos mais reativos da corrente de matéria-prima.
A BASF também oferece catalisadores de hidroprocessamento semelhantes aos que as refinarias de petróleo usam para substituir enxofre por hidrogênio. “Na verdade, otimizamos o catalisador para garantir que ele seja adequado para serviços em óleos de pirólise de plástico”, diz Vityuk. “Não é um copiar e colar da área de refino.” Por exemplo, em vez de se concentrar no enxofre, os catalisadores ajudam a remover o nitrogênio, que está em plásticos como o nylon.
Steve Deutsch, consultor do Catalyst Group, diz que a variabilidade do óleo de pirólise é um problema que a indústria precisará resolver. Embora existam padrões para as matérias-primas do cracker de etileno, “não há nada semelhante para o óleo de pirólise”, diz ele. “A indústria precisa evoluir de forma a se tornar mais padronizada.”
As empresas petroquímicas estão começando a construir infraestrutura para processar os produtos das plantas de pirólise. A Shell está construindo atualizadores em seus complexos químicos em Moerdijk, Holanda e Cingapura, para remover contaminantes do óleo de pirólise de terceiros. Cada um será capaz de manusear 50.000 t de óleo por ano.
“Devido ao estágio incipiente da indústria de reciclagem química, podemos esperar uma grande variação na qualidade do óleo de pirólise, em que a etapa de atualização se torna parte integrante do aumento das quantidades utilizáveis”, diz Philip Turley, gerente geral global de circularidade de plásticos da Shell .
A Shell já bloqueou suprimentos de várias empresas que podem fornecer óleo de pirólise aos atualizadores. Por exemplo, ela investiu na BlueAlp e as duas planejam construir 30.000 t por ano de capacidade de pirólise de plásticos na Holanda. A Shell também tem um acordo de compra com a Pryme, outra empresa europeia de pirólise.
Da mesma forma, a Dow está trabalhando com a empresa de engenharia Topsoe para construir uma unidade de purificação de óleo de pirólise em seu complexo em Terneuzen, na Holanda. Assim como a Shell, a Dow diz que sua unidade visa purificar e homogeneizar matérias-primas provenientes de uma variedade de plantas de pirólise. “Alguns têm uma matéria-prima que ainda precisa ser limpa ou processada antes que você possa colocá-la em um cracker. Alguns nem conseguimos olhar”, diz Lahoti, apontando para aqueles com alto teor aromático e naftaleno.
“Quando você sai da fase de start-up, que é onde muitas dessas empresas estão, você começa a pensar em como essas tecnologias se encaixam na indústria química”, diz Lahoti. “E é aqui que uma empresa como a Dow permite que algumas dessas start-ups sejam bem-sucedidas porque trazemos nossa experiência em tecnologia, nossa experiência de processamento e ajudamos a inserir alguns desses feeds em nosso sistema.”
A TECNOLOGIA EVOLUI
Lahoti diz que os próprios processos de pirólise estão evoluindo para se adequar melhor à indústria petroquímica. Ele vê “uma transição da pirólise convencional para diferentes tecnologias, algumas das quais foram construídas com base na pirólise convencional, mas avançaram a um ponto em que não é apenas pirólise”.
Por exemplo, Lahoti não considera a tecnologia de Mura como pirólise. O principal desenvolvimento é o vapor supercrítico, que transfere calor diretamente para as partículas de polímero. Na pirólise comum, o calor vem do forno e é transferido por partículas de plástico pouco condutoras. “Quanto maior você faz o forno, mais difícil fica para o calor chegar lá”, diz Lahoti.
As empresas também estão introduzindo catálise nos próprios reatores de pirólise. Além de diminuir a energia de ativação do processo, os catalisadores podem ajustar a saída para produtos mais desejáveis. Após a pirólise, você fica com algumas moléculas com 40 ou 50 carbonos – grandes demais para alimentar um cracker diretamente, diz Deutsch, do Catalyst Group. “Com a pirólise catalítica, você pode tornar essa distribuição mais estreita e mais leve.”
Desde 2020, a LyondellBasell opera uma planta piloto em Ferrara, Itália, para testar sua tecnologia de pirólise catalítica, chamada MoReTec. Embora a empresa não tenha dito quais catalisadores está testando, muitos grupos de pesquisa de pirólise estão trabalhando com catalisadores de zeólita, como o ZSM-5, que são comumente usados no refino.
Um sinal claro de que o interesse pela pirólise está decolando é que grandes indústria de engenharia estão licenciando tecnologias para terceiros que querem entrar no negócio. A KBR está licenciando o processo de Mura. A Lummus Technology está comercializando uma tecnologia da New Hope Energy. E no final do ano passado, a Honeywell UOP revelou seu próprio processo, chamado UpCycle.
Kevin Quast, líder de negócios global para o negócio de circularidade de plásticos da Honeywell, diz que a reputação da Honeywell UOP é uma grande ajuda no mercado. “As pessoas gostam do nome UOP”, diz ele. A indústria “está muito familiarizada com esses tipos de tecnologias e é capaz de levar algo da escala piloto para a escala comercial”.
A UOP comprou os direitos de um processo que vinha sendo executado na Europa há vários anos na década de 1990. A empresa vem pilotando e refinando há 2 anos e meio.
Quast observa algumas diferenças importantes entre o UpCycle e outros sistemas de pirólise. Por exemplo, a Honeywell UOP tem uma etapa de pré-tratamento na qual seleciona os plásticos certos para o sistema e os derrete antes de irem para o reator principal. O que sai é uma fração leve, como nafta e diesel, além de um corte mais pesado. A corrente mais pesada pode ser enviada para um cracker catalítico fluidizado para fazer propileno.
A Honeywell UOP está formando duas joint ventures, uma na Espanha com a indústria de infraestrutura Sacyr e outra no Texas com a recicladora Avangard Innovative. A Honeywell UOP também está licenciando o processo para plantas na China e na Turquia.
A escala das plantas Honeywell UOP – 30.000 t por ano – é um “ponto ideal” para a quantidade de matéria-prima que pode ser coletada em uma cidade de médio porte, diz Quast. Ele questiona se algumas das maiores plantas de pirólise que foram anunciadas poderão adquirir matérias-primas economicamente.
Outro sinal de que a pirólise está atingindo o grande momento é que uma das maiores indústria de petróleo do mundo, a ExxonMobil, está fazendo um esforço . No próximo mês, a empresa concluirá uma instalação de pirólise em seu complexo petroquímico em Baytown, Texas, com capacidade para processar 30.000 t de plásticos por ano.
“Na verdade, estamos processando os resíduos plásticos diretamente em nossas próprias instalações”, diz Natalie Martinez, gerente de negócios feed-to-value da ExxonMobil. Ela se recusa a fornecer mais detalhes sobre o equipamento que está sendo usado ou o pós-processamento envolvido.
Colocar a pirólise de plásticos em um complexo petroquímico permite que a ExxonMobil use gases que os sistemas autônomos precisam consumir como combustível, diz Martinez. “Tudo o que está saindo do processo está sendo utilizado em uma instalação integrada”, diz ela.
A ExxonMobil tem uma joint venture com a indústria de pirólise Agilyx, chamada Cyclyx International, que se dedica a encontrar matéria-prima para a planta. A ExxonMobil está explorando a classificação óptica e a análise avançada para gerenciar as grandes quantidades de material que serão direcionadas para lá. “Você não pode apoiar isso com a classificação manual”, diz Martinez.
Se uma grande indústria de petróleo e química como a ExxonMobil puder operar o processo com sucesso em larga escala, será a refutação final dos opositores da pirólise. A empresa pretende implantar a tecnologia em fábricas em todo o mundo para atingir a meta de reciclar 500.000 toneladas de plásticos anualmente até o final de 2026.
“Sabemos que a escala, e ser capaz de fazer isso globalmente, será realmente a chave para o sucesso final”, diz Martinez. “Não são apenas os aspectos técnicos do processamento de resíduos plásticos. Sabemos que isso é alcançável e factível. É uma escala que será significativa e fornecerá uma solução para a sociedade.”