Em Akron, Ohio, situado entre prédios industriais e centros de serviços automotivos, há um pequeno oásis de aço polido e andaimes antiderrapantes. Os proprietários desta nova instalação esperam que seja o futuro da indústria de plásticos .
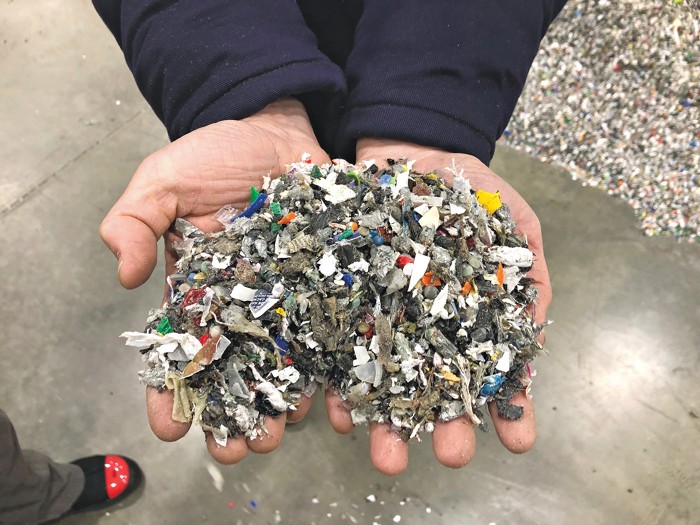
Indústria de plásticos vê início sustentável em fábrica em Ohio
A instalação, uma planta de pirólise administrada pela Alterra Energy, decompõe os resíduos plásticos em uma mistura semelhante ao petróleo bruto que pode ser alimentada em plantas petroquímicas e transformada novamente em novos plásticos.
A planta pode processar cerca de 60 toneladas métricas (t) de plásticos por dia. Era a maior planta operacional de pirólise de plásticos nos Estados Unidos até recentemente, quando foi superada por uma instalação maior que a ExxonMobil iniciou em Houston. Muitas outras plantas de pirólise, incluindo aquelas que usam a tecnologia da Alterra, estão em pranchetas para locais em todo o mundo.
Jornalistas visitaram a fábrica da Alterra em novembro durante uma viagem organizada pelo American Chemistry Council, um grupo comercial interessado em promover a reciclagem de plásticos por pirólise, despolimerização e outras técnicas emergentes que a indústria chama de reciclagem avançada. A indústria almeja que tais tecnologias se consolidem e, assim, melhorem a imagem da indústria de plásticos.
Jeremy DeBenedictis, presidente da Alterra, disse ao grupo em uma sala de conferências nos escritórios da fábrica que ele tem aspirações ousadas. “É uma pequena quantidade de material agora”, ele reconheceu. As plantas de polimerização que produzem novos plásticos são muito maiores. Mas DeBenedictis rapidamente mudou para uma marcha otimista, observando que, uma década atrás, a Tesla fabricava apenas alguns milhares de carros por ano. “Você sabe quantos eles vão fazer no ano que vem? Dois milhões. Novas tecnologias chegarão lá quando forem adotadas pelo público e pela indústria.”
DeBenedictis ingressou na Alterra na época em que a Tesla estava apenas começando a construir carros. Em 2011, ele era gerente da General Electric, administrando uma empresa de fabricação de alvos para scanners de tomografia computadorizada e máquinas de raio-X. Ele queria tentar administrar uma start-up, então ingressou na Alterra, então conhecida como Vadxx Energy. Na época, era um equipamento de três funcionários com um reator de mesa, que literalmente ficava em uma garagem, capaz de processar cerca de 2 kg de lixo plástico por hora.
Dezenas de pequenas empresas como a Alterra em todo o mundo estão desenvolvendo processos de pirólise de plásticos. As instalações que estão construindo destinam-se a resolver um dilema . A reciclagem mecânica convencional, na qual os plásticos são coletados, separados, lavados e derretidos para reutilização, tem suas limitações. Notavelmente, os fluxos de resíduos plásticos devem ser relativamente homogêneos.
Assim, a grande maioria dos plásticos reciclados nos EUA são garrafas e recipientes de polietileno de alta densidade e tereftalato de polietileno, que são fáceis de classificar. Não é de admirar que a taxa geral de reciclagem de plásticos nos EUA tenha lutado para quebrar 9%; a maior parte do resto vai para um aterro sanitário.
Em comparação com as instalações de reciclagem mecânica, as plantas de pirólise podem receber uma variedade maior de plásticos, incluindo filmes e embalagens flexíveis. Eles também são mais robustos quando se trata de lidar com a mistura de plásticos que ocorre quando diferentes materiais são usados em embalagens ou combinados no fluxo de reciclagem. Todos os plásticos se decompõem juntos no mesmo forno.
Ainda assim, as matérias-primas preferidas para plantas de pirólise são poliolefinas, como polietileno e polipropileno, e poliestireno. Os operadores da usina tentam eliminar, às vezes separando-os fisicamente, os plásticos que contêm cloro, oxigênio e nitrogênio – como cloreto de polivinila (PVC), tereftalato de polietileno e náilon – na medida do possível para minimizar as impurezas que não sejam hidrocarbonetos em seu produto final. produtos.
O antepassado da Alterra, Vadxx, foi fundado pelo inventor William Ullom em 2009, quando ele comprou os direitos das patentes da Universidade de Wyoming. Eles foram um ponto de partida. Trabalhando naquela garagem, Ullom e outros engenheiros da Vadxx fizeram alterações no processo até que tivessem algo próprio. A Alterra agora tem três patentes e quatro pedidos de patente.
DeBenedictis disse que os engenheiros decidiram tornar a operação contínua. A maioria dos outros processos de pirólise em desenvolvimento são centrados em reatores bateladas, que são menos eficientes. A Alterra também manteve o processo simples evitando o uso de catalisadores para auxiliar na reação de pirólise.
Para demonstrar como a planta de Akron é onívora, DeBenedictis pediu aos repórteres que trouxessem detritos de plástico para jogar no reator de pirólise. Um repórter recolheu detritos de seu quarto de hotel: as sacolas plásticas que cobrem os copos, o próprio copo plástico, a embalagem do sabonete.
Alterra cresceu fora da garagem. A instalação de pirólise, iniciada em 2020, emprega 32 pessoas e possui todas as características de uma fábrica química tradicional, com tubos, conexões e vasos interligados. Os visitantes devem usar capacetes, óculos de segurança, protetores de sapato com biqueira de aço e macacões resistentes ao fogo antes de serem permitidos no chão de fábrica.
A área de escritórios se abre para um bunker de concreto que pode armazenar 500 t de resíduos plásticos. DeBenedictis disse que a empresa paga uma “pequena quantia” por sua matéria-prima, 50% a 75% da qual vem de instalações do meio-oeste que processam o que os residentes jogam em suas lixeiras. Cerca de 80% do material chega triturado e adensado pela Ravago, distribuidora e recicladora de plásticos que investiu na Alterra.
O restante são resíduos pós-industriais, como cortes da fabricação de fraldas ou pedaços de canos feitos de polietileno reticulado. Esses tipos de materiais, disse Kevin Dressler, diretor de licenciamento da Alterra, não podem ser reciclados mecanicamente e, caso contrário, iriam para um aterro sanitário.
No bunker, os plásticos, predominantemente polietileno e polipropileno, estão amontoados em pilhas cinzentas salpicadas aleatoriamente de cores. Fragmentos de rótulos de embalagens podem ser vistos nos pedaços de plástico triturados e compactados. Indústria
Um carregador frontal joga os fragmentos em uma tremonha e uma correia transportadora os transporta para uma extrusora. O plástico sai da extrusora com a consistência de caramelo salgado e é enviado por cano para o reator. O objetivo da etapa de extrusão é aquecer o plástico e dar-lhe uma densidade uniforme para que ele possa transferir o calor de forma previsível no reator de pirólise.
Nesta fase, o plástico é misturado com óxido de cálcio, que remove o cloro do PVC errante. O cloro pode corroer e danificar o equipamento de produção química dos clientes a jusante se permanecer no óleo de pirólise. DeBenedictis disse que o óxido de cálcio reage com o cloro para formar cloreto de cálcio, removendo cerca de 80% do halogênio. Os clientes lidam com o restante atualizando quimicamente o óleo de pirólise.